Total Quality Management Value
“Total Quality Management” or “TQM” is a term, that consists of all the organization-wide efforts for installing and making the appropriate climate for each of the organizations to improve their ability to deliver only high quality products as well as services to their customers. After the period, when the developed countries of Western Europe as well as North America had problems in their economy, because of having so many competitors from Japan, they had to manage to continue their work producing the high quality products at a competitive price. In this period, the United Kingdom for the first time in a long period after the start of the Industrial Revolution, became a net importer of the finished goods and the United States undertook their own soul-searching. Companies in the early 1980s began re-examining the quality control techniques, which were invented during the last 50 years, using those previously developed techniques, which had been so successfully employed by the Japanese.
In the spring of 1984 some of the civilian researchers in the United States of America were asked to assess the statistical process control and so to give recommendations on how to apply the offered approaches for improving the Navy's operational effectiveness in the USA. The given recommendation was to adopt the teachings of Edward Deming and so in 1985 the Navy branded this effort as "Total Quality Management". From the Navy, “Total Quality Management” spread throughout the United States Federal Government, resulting in the creation of the Malcolm Baldrige National Quality Award in August 1987, the creation of the “Federal Quality Institute” in June 1988 and the adoption of “Total Quality Management” by the government as well as the armed forces, such as the United States Coast Guard, the United States Department of Defence and the United Army.
The “Total Quality Management” principles can be used not only as the means to recapture the market share from the Japanese people, but also to help remain competitive while the bidding for contracts from the Federal Government. The "total quality" requires to involve the suppliers (not only employees) in the process of improvement efforts creation. There is no set definition about what “Total Quality Management” truly is and what exact actions it requires from the companies and the organizations, but a review of the original United States Navy effort gives an understanding of what is involved in the term of “Total Quality Management”.
The key concepts in the “Total Quality Management” effort include the statements, that the quality is defined by the customers' requirements, the increased quality comes from systematic analysis and improvement of work processes, the top management has direct responsibility for quality improvement and that the quality improvement is a continuous effort and conducted throughout the organization.
The Navy used the special techniques and tools, such as the so-called “PDCA” cycle to drive issues to resolution, the ad hoc cross-functional teams (which are similar to and can remind of the so-called “quality circles”) are responsible for addressing immediate process issues, that all of the standing cross-functional teams are also responsible for the processes improvement over the long term, that active management participation through steering committees, the use of so-called “Seven Basic Tools of Quality” for analysing the quality-related issues has to be applied within the “Total Quality Management”.
The mentioned above “Seven Basic Tools of Quality” is a fixed set of graphical techniques, which can be identified as being most helpful in so-called “troubleshooting” issues. This term is related to another term – “quality” and it’s well known among those who deal within the “Total Quality Management”. These tools are called “basic” for a reason of them being suitable for people with a little formal training in statistics. Also they are called “basic”, because they can be used for the purpose of solving the vast majority of quality-related issues. These “Seven Basic Tools of Quality” are: “Check sheet”, “Control Chart”, “Histogram”, “Cause-and-effect diagram”, “Pareto chart”, “Scatter diagram” and “Stratification”.
In 1950 companies that had set about training their workforces in the quality control (the statistical quality control) found, that the complexity of the subject intimidated the vast majority of their workers and scaled back training for focusing primarily on the simpler methods, which suffice for most quality-related issues. So these “Seven Basic Tools” can be put in contrast to more advanced statistical methods. The other methods include “survey sampling”, “acceptance sampling”, “statistical hypothesis testing”, “multivariate analysis”, “design of experiments” and other methods, which were developed in the field of operations research. Also these “Seven Basic Tools of Quality” was referenced by the “Project Management Institute” in a so-called “Guide to the project management body of knowledge”. They were given as an example of the general useful tools for controlling project quality and planning project quality.
The “Total quality management” includes all together eight main elements, which are “focusing on the customers”, “total employee involvement”, “process-centred”, “integrated system”, “strategic and systematic”, “continual improvement”, “fact-based decision making” and “communications” approaches. These, described above elements, are essential in “Total Quality Management” and many companies define them as the core principles and values, which these companies have to take into consideration as the “Total quality management” contains enterprise-wide tools for implementing and making durable the atmosphere, in which an organization infinitely improves its ability to deliver the high-quality products as well services to its customers.
The “Total Quality Management” solution is the one among other solutions, which you can find in ConceptDraw STORE to use while working in ConceptDraw DIAGRAM and which can help you and your organization display your business and industrial processes using mind maps and making “Total Quality Management” diagrams, and so to demonstrate the quality control in a visual manner.
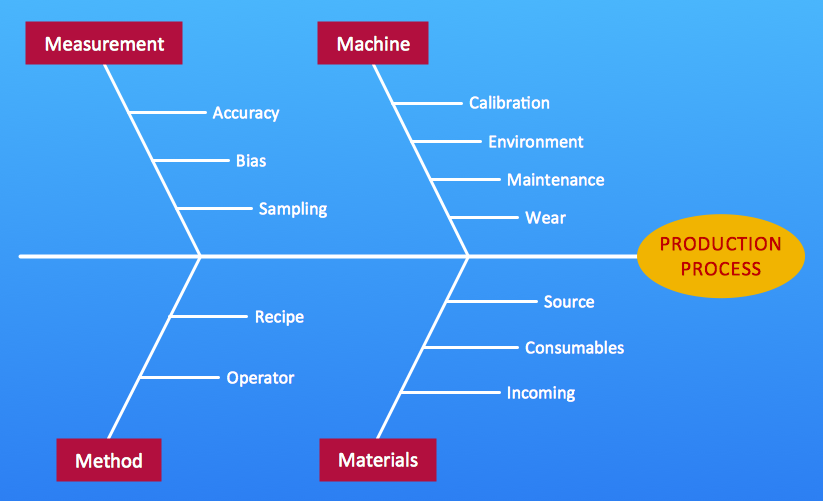
Pic.1 Fishbone diagram 4M: Production process.
In the total quality management (TQM) fishbone diagram (Ishikawa diagram, herringbone diagrams, cause-and-effect diagrams, Fishikawa) represents factors (reasons) which influence on quality coefficient of the final result of the concerned process. The main factors are 4M:
- Men
- Methods
- Materials
- Machines
These main factors are subdivided into smaller. The degree of the detailed elaboration is defined only by factors significance and planner’s tasks. With the help of Ishikawa diagram it is possible to show visually all factors which influence on the quality coefficient, sort them out and show their interrelation.
See also Samples:
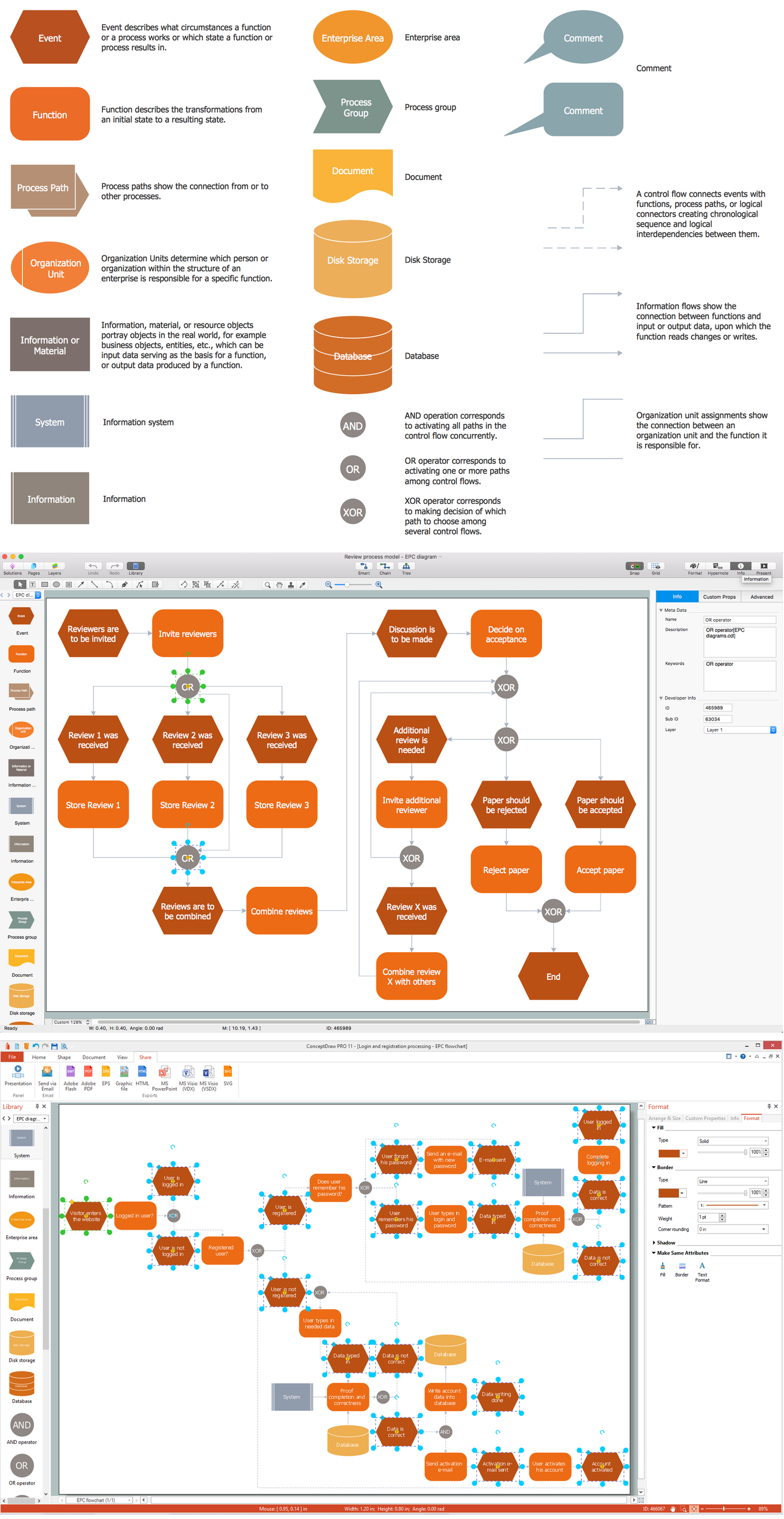
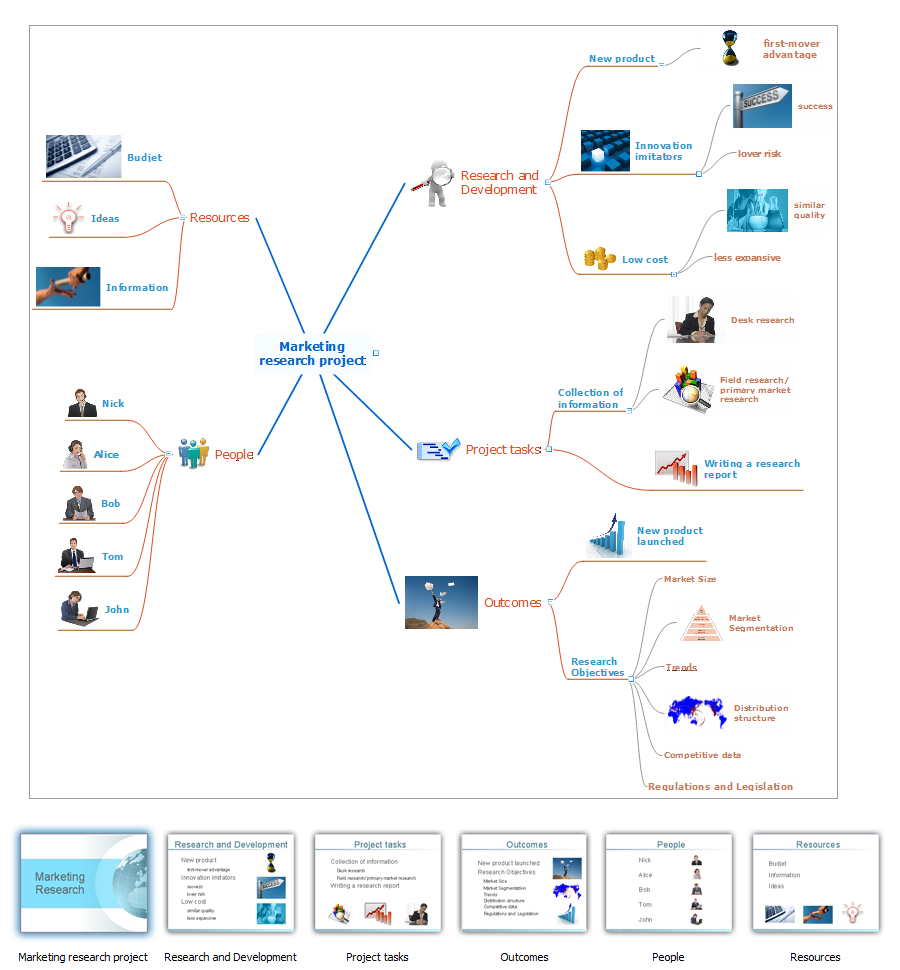
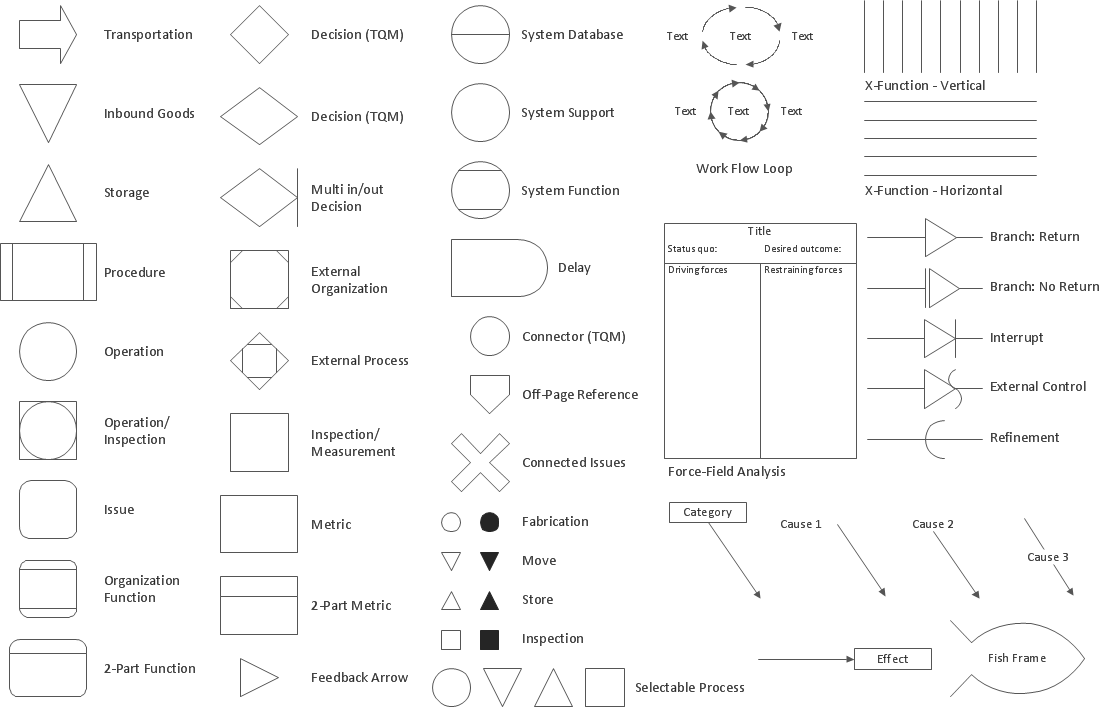
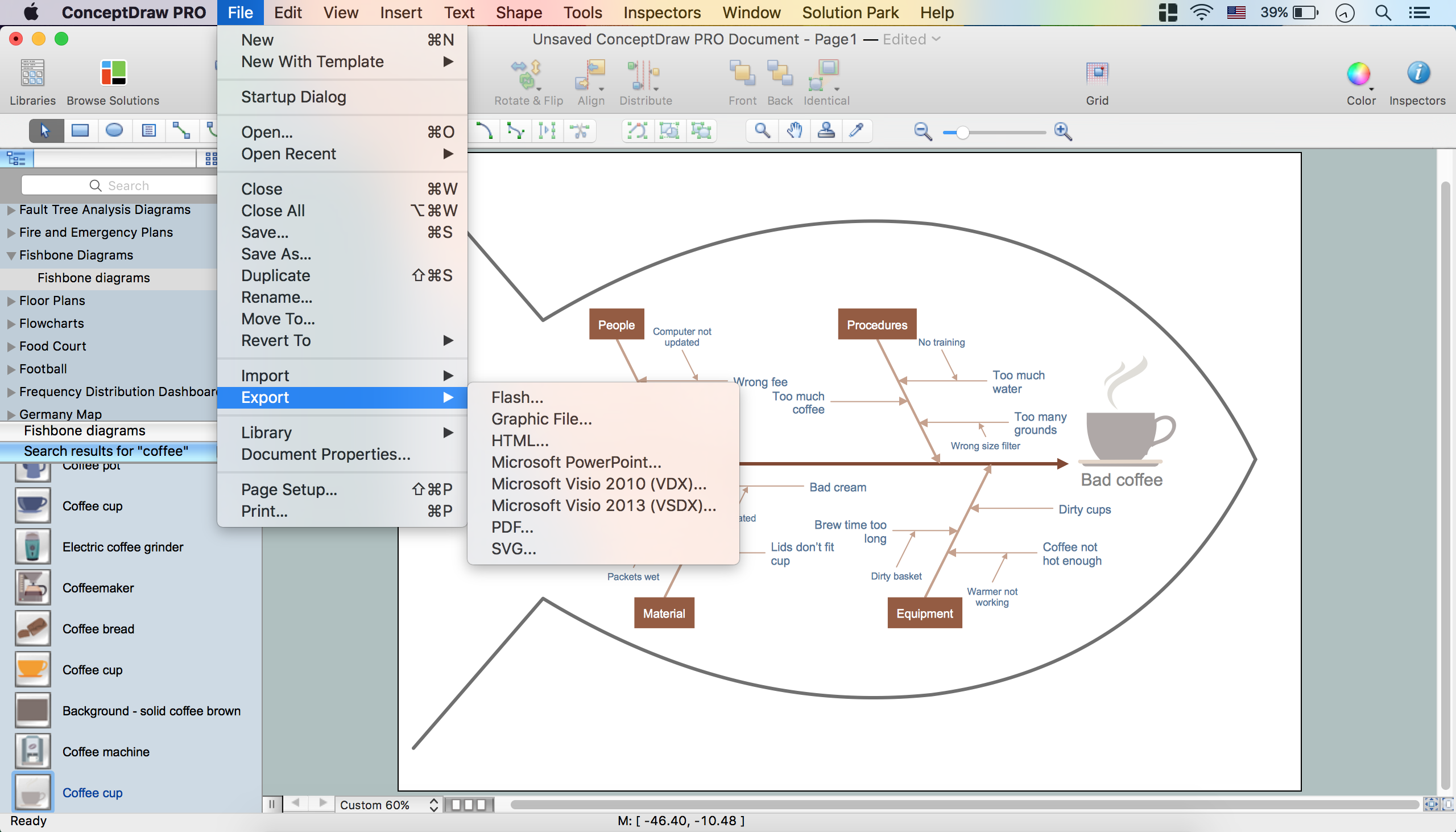
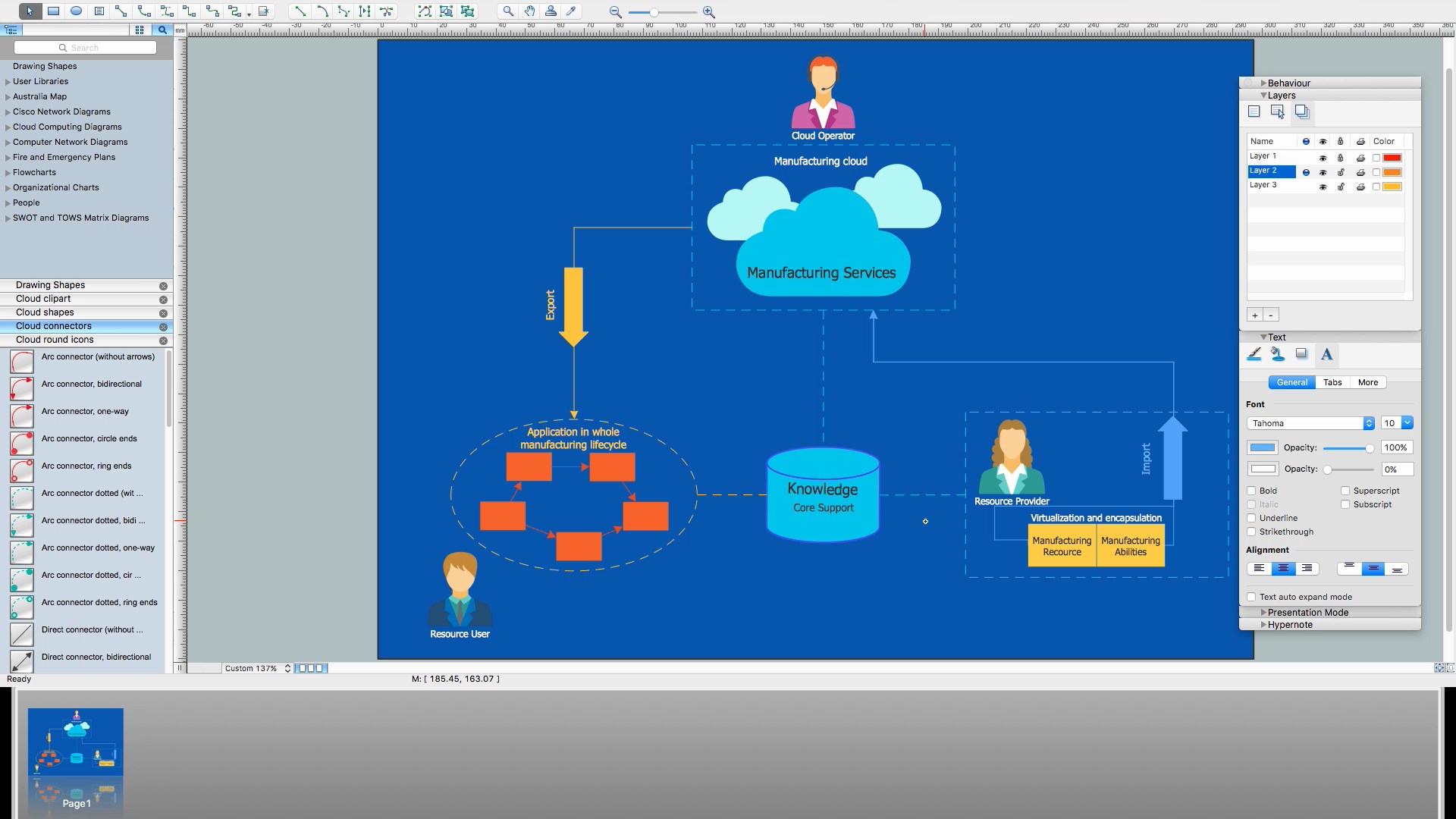
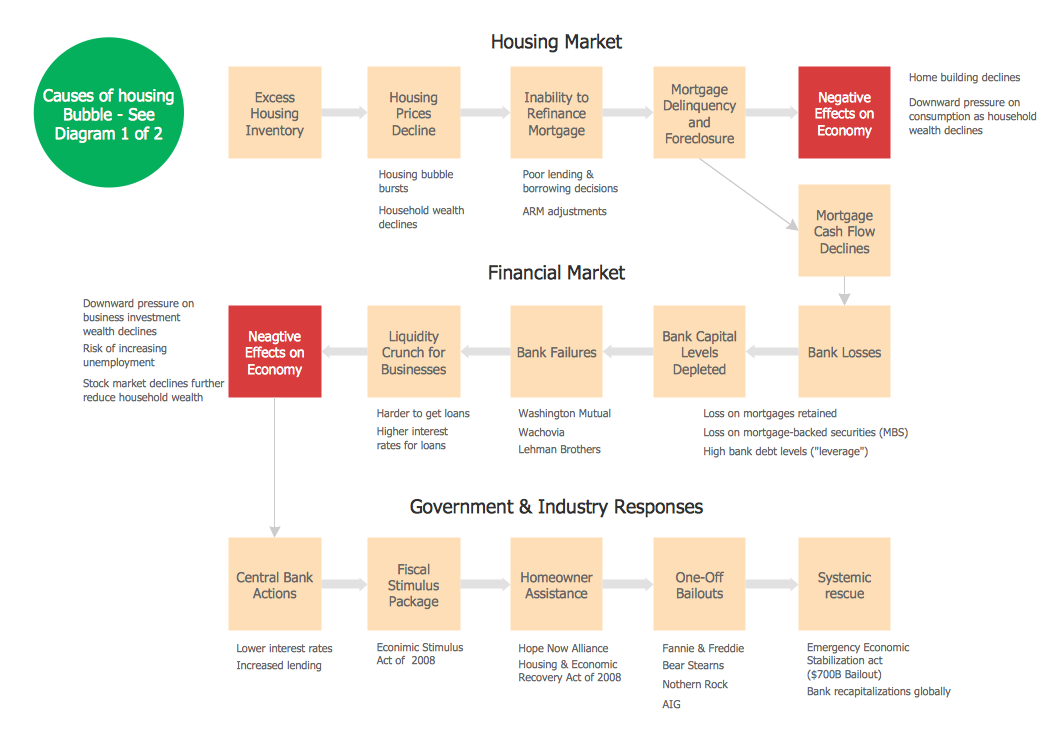
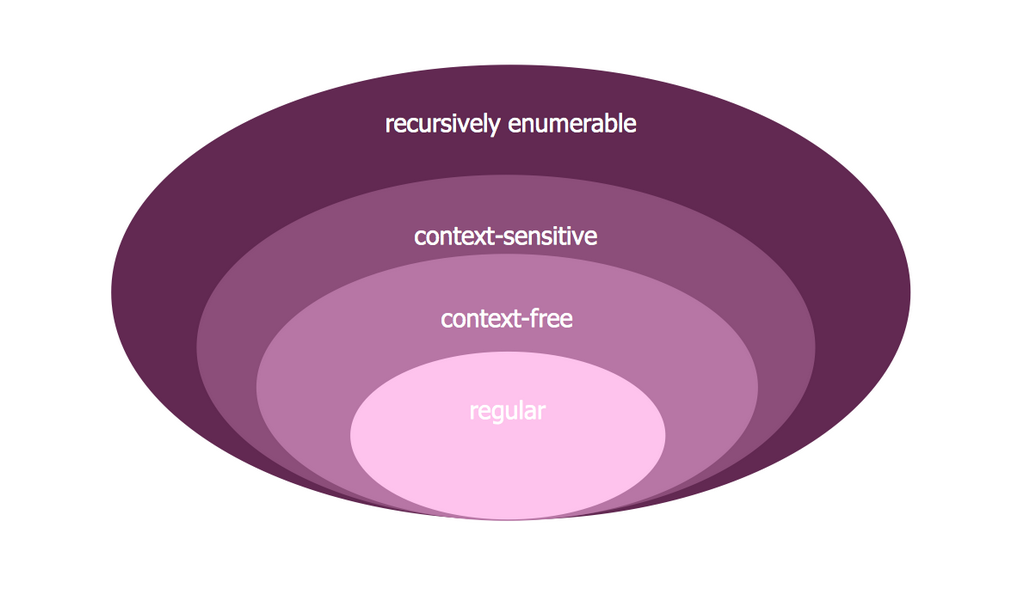